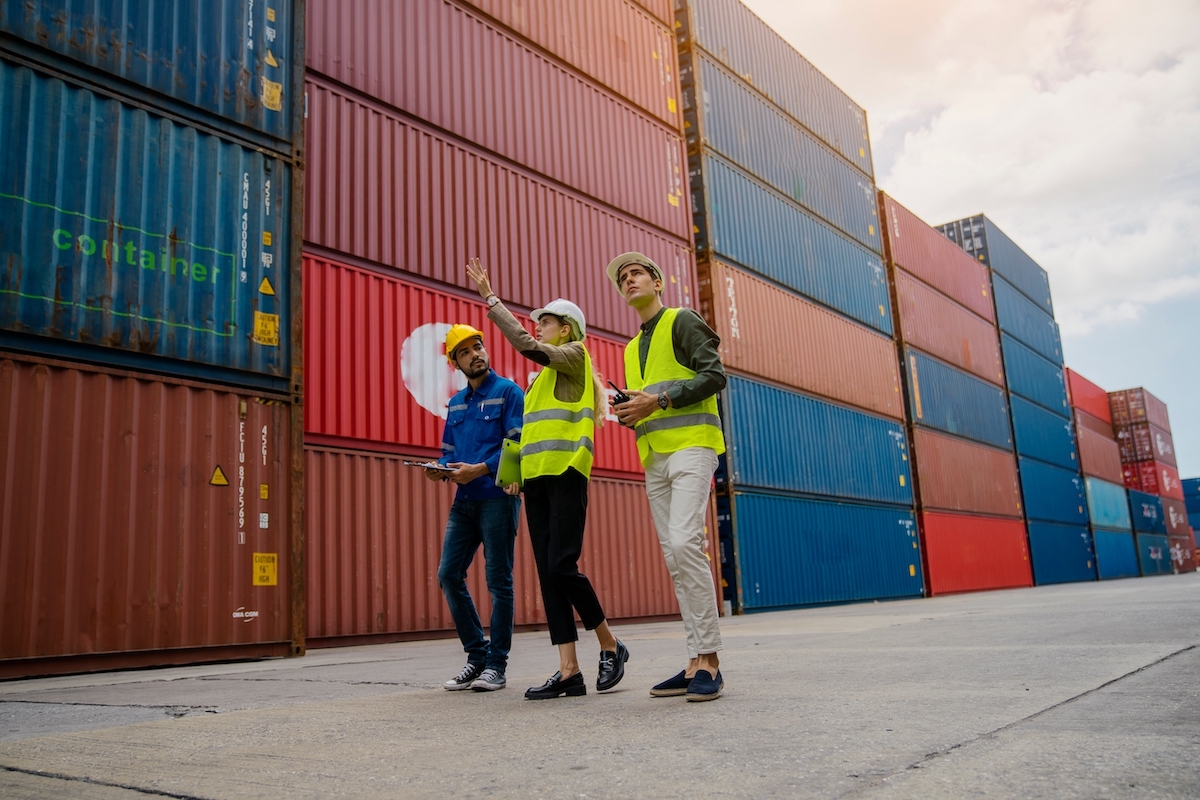
Discover what strategies build resilient and agile supply chains in 2023 to overcome material shortages and deal with sector backlogs. Get a research-backed overview of the best practices and organisational factors to take your supply chain capability to the next level.
There's been a storm of change in the supply chain sea's in the last few years, with a wave of events (pandemic lock-downs, freight slow-downs, the Ukraine war, energy supply issues, effects of Brexit and other cross-border customs issues) causing global and regional disruption and reverberations through many industry sectors. This has created many challenges for supply chain professionals to confront and overcome, and has highlighted just how important a positive investment in building a resilient and agile supply chain is for manufacturers.
Unfortunately, it seems troubled waters still may lie ahead, as raw material costs are identified as the number one supply chain threat by 71% of global companies (KPMG, 2022) for the upcoming year. The need to pursue key strategies to build a resilient supply chain that can combat material shortages, frequently changing component lead times, and deal with sector backlogs, has never been greater. Two-thirds of business leaders in the same KPMG Global Supply Chain Trends survey stress the need to focus on and provide visibility into the supply chain to improve operational resilience in the future.
Firstly, let's look at the challenges and models we can use to assess organisational capability, then move on to what we can consider to build capacity. Finally, we'll uncover the key components of resilient supply chains.
Sourcing and supply chain threats in 2023
The increased volatility due to recent events has created a premium on upgrading all supply chain capabilities — with increased flexibility, reliability and agility — to respond proficiently to these challenges.
Raw materials costs and components shortages are being affected due to capacity-impacting issues, and concomitant inflation issues. Keelvar's whitepaper Turning Chaos into Control, states that 83% of supply chain professionals identify 'overcoming supply chain disruptions' at the top of their agenda, followed by 'combating inflation and rising costs' (77%), 'managing market volatility' (74%), and 'managing geopolitical risk' (71%).
Evolving a company's supply chain strategy from reactive to responsive and through to the truly resourceful (see image below) — where planned and unplanned risks can be managed without strategic perma-crisis — is paramount in combatting these challenges.
Transportation costs are rising with energy prices, materials costs, customs and border issues. Inflation and capacity shortages are putting significant pressures on upstream supply chain (particularly in freight transportation, with tenfold increases in container delivery pricing in some areas).
The legacy of COVID-19 includes a record level of order backlogs, alongside amplified demand fluctuations. Sourcing processes need to be quicker, have increased fidelity (less errors), and be flexible (less rigidity with SLAs, and ongoing review processes). Data-driven decisions provide insight into strategic and tactical decision-making relevant to changing market conditions.
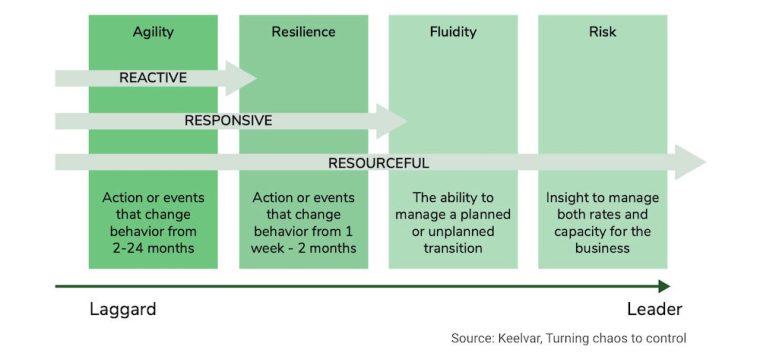
6 steps to build supply chain resilience
— Focus on core products and services to mitigate risk. — Move from Just-In-Time to Just-In-Case inventory. — Develop pro-active supply and sourcing plans — Harness realtime analytics and forecasting. — Embrace innovation for transparency and efficiency. — Illuminate your supply chain through end-to-end visibility and transparency.
Focus on core products and services to mitigate risk
Much like a ship's captain who prioritises the safety of their crew and cargo, supply chain professionals need to concentrate on managing high-demand, critical items that are vital to the operation of production lines. Double down on robust inventory planning and component sourcing agility. Consider working with a trusted master supplier and address dual sourcing, and regional distribution strategy.
Move from Just-In-Time to Just-In-Case inventory
Uncertainty is inevitable as disruptive factors persist in the global economy. Shift from Just-In-Time to Just-In-Case by readjusting buffer levels, holding extra inventory for critical items, and engaging with your supply network to front-run any upcoming delays or supply issues. Many supplier lead times have become elongated as backlogs continue from the pandemic, etc. Active inventory management can resolve redundancy, and stop stock levels going out of control, taking into account local risks for your specific manufacturing needs.
Develop pro-active supply and sourcing plans
A skilled captain always has a backup plan. Identify potential alternative vendors to work around issues (a master supplier such as Acorn usually has a better, extended network to leverage). Consider component work-arounds, substitutions, or consolidation through a supply chain product design process.
Harness realtime analytics and forecasting
Like a seasoned navigator reading the stars, supply chain professionals now have a much greater ability to implement and aggregate real-time data analytics to improve the accuracy of predictions and forecasts of demand volatility. The supply chain can be steered towards efficiency and success by sharing these insights with your sales and operations teams to streamline fulfillment and execution frameworks, and manage demand.
Embrace innovation for transparency and efficiency
The winds of change bring new technologies, to enhance product transparency, prevent counterfeiting and ensure product quality, as well as the ability to automate workflows through better tracking and transparency (blockchain, digital twins and smart contracts are also coming into play). Embrace these innovations and map out an appropriate adoption of these supply chain management technologies with a logistics expert who can aid you in making the transition.
Illuminate your supply chain through end-to-end visibility and transparency
Just as a lighthouse guides ships through treacherous waters, end-to-end visibility and transparency are essential for navigating the complexities of modern supply chains. In a 2022 McKinsey Global Supply Chain Leaders survey, 45% of survey respondents reported they either have no visibility into their upstream supply chain, or that they could only see as far as their first-tier suppliers. When you shed more light on your supply chain by extending your efforts to increase visibility across procurement, storage management and delivery, operational stability is maintained and improved.
Further research (which to some extent overlaps with this McKinsey research) suggests how to enhance these steps: Gartner has highlighted 6 practical strategies for building supply chain resilience:
— dual and alternate supply planning with multi-sourcing.
— factoring regional and local delivery through near-shoring.
— inoculating against supplier difficulties through manufacturing network diversification.
— optimising stockholding with inventory and capacity buffers.
— focusing on core strengths through platform, product or plant harmonisation.
— enhancing operational strengths through ecosystem partners.
3 key components for resilient supply chain planning
We promised to uncover the key components for a resilient supply chain — and the McKinsey Research is clearest in suggesting these three key components are the most effective path to supply chain resilience: greater visibility, scenario planning, and mastering data.
1. The guiding light of greater visibility
Implementing digital dashboards for end-to-end supply chain visibility enables better management of supply chain effectiveness and prevents disruption-related problems. Greater clarity and smart intelligent business decisions can be made with the right information at your fingertips. McKinsey reports that 66% of organisations that have implemented them are twice as likely to avoid disruption-related issues.
2. Charting a course with scenario planning
Robust scenario planning is like a map of potential obstacles and opportunities allowing you to anticipate potential disruptions and develop strategies and alternative routes to mitigate their impact. A course can be charted with confidence when various scenarios have already been considered and plans are in place to meet them. Sound scenario planning cuts supply chain disruption in half with the 37 percent of surveyed companies that utilise it (McKinsey).
3. Quality data acts as your compass
A ship needs to keep accurate direction in any wind, and so does your supply chain planning. Ensure high-quality, accurate, and comprehensive master data to support both visibility and effective scenario planning. Only 53% of companies have this solid foundation in place, the other half steering ahead more blindly. Those with sufficient quality data are 1.5x more likely to report no challenges from recent supply chain impacts (McKinsey).
Voyaging toward supply chain resilience
As we navigate the uncharted waters of 2023, for most of us things are calmer after the storms of recent years, but all is not yet smooth sailing.
By applying these strategies, supply chain professionals can better steer their organisation through economic headwinds and the tempest of delivery issues, with an increased confidence and capability in managing material shortages and disruptions. Cultivating a strong ecosystem also provides a safe harbour of supplier networks and partnerships to rely upon when the weather turns.
Sources: — KPMG global supply chains trends survey — McKinsey Survey of global supply chain leaders — Gartner: 6 strategies or a resilient supply chain — Keelvar: Turning chaos to control 2022 sourcing whitepaper
Chris Till, MD – Acorn Industrial Components, has been involved in OEM logistics for 35+ years. Along the way, he's developed a wealth of experience setting up and running supply chains for clients from Brighton to Chung-Do, helping them not just survive, but to thrive in the global manufacturing world.
Learn about our inventory planning
Inventory Management & Analysis is essential for the best balance of stockholding, demand and sourcing processes to meet your manufacturing goals. We work with you to create a more resilient supply chain.