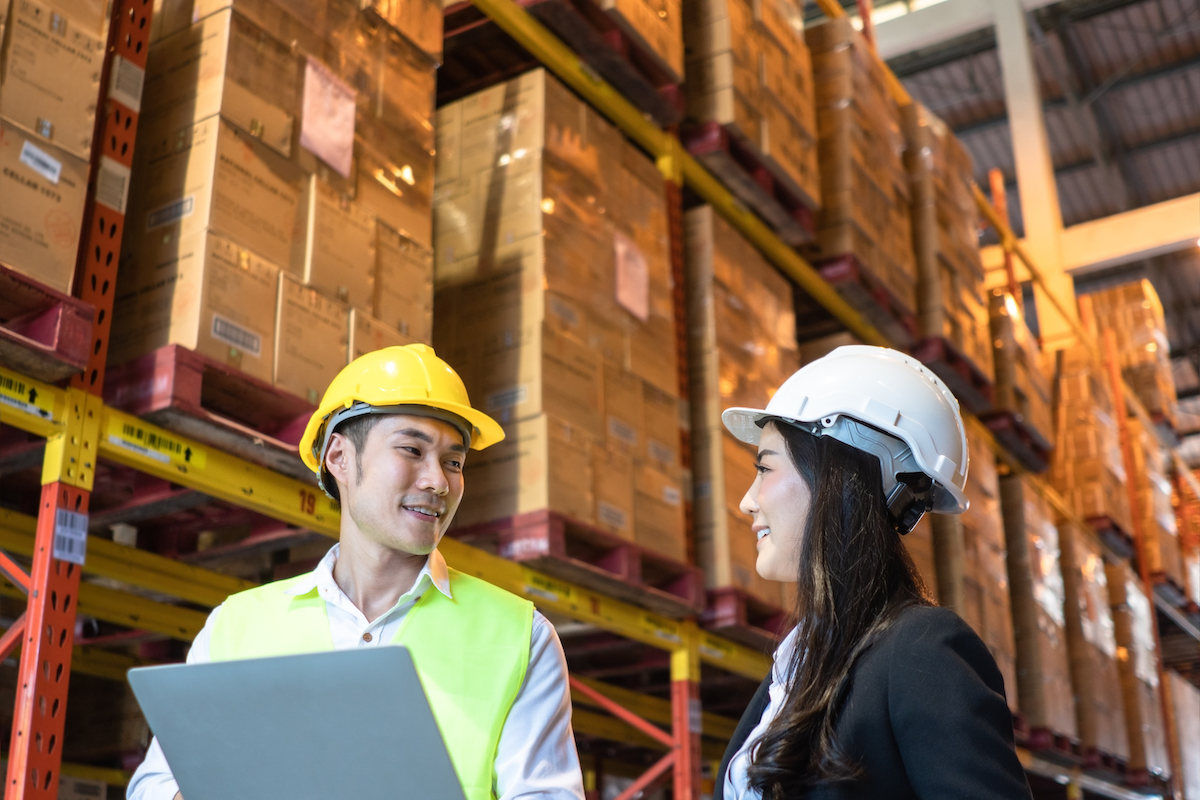
No manufacturer wants excess inventory. Inefficient, and the bane of lean manufacturing, inventory also needs to be balanced against the threat of stock-out and line-downs. Multiple reasons can be attributed to why excess inventory in manufacturing builds up.
There's the perennial problems of procurement, system and management inefficiencies (more on these below). Then there's also the unique recent events that have caused a risk aversion to lean inventory due to the pandemic, Houthi rebels disrupting cargo ship routes, the Ukraine crisis, semiconductor shortage, China lockdown, et cetera. The list goes on.
Inventory build-up leads to additional capital, service and storage costs, along with shrinkage, obsolescence and other inventory loss. According to Zebra, inventory costs can be cut by 10% by reducing stock-outs and eliminating over-stocking with excess inventory. Let's examine the upsides and downsides in more detail, and get into the causes, consequences and how to mitigate excess inventory problems.
Benefits of Reducing Manufacturing Component Inventory
Reducing the level of inventory you keep on hand provides several advantages for your company's supply chain. With lower stock levels, you can expect these headline benefits:
Cost reductions
Storing components in the warehouse (your own, or an outsourced warehouse service) ties up valuable capital that could be put to better use elsewhere. Trimming inventory cuts the expenses associated with facilities, utilities, insurance and more. The company's bottom line will improve as capital isn't locked up in unproductive ways.
Less waste
Excess materials carry risks like damage, expiration and degradation over time. Limiting stockpiles also reduces the chance items don't become redundant or obsolete, and thus becoming waste. This has the added benefit of benefitting your ESG targets, and reducing emissions associated with additional stockholding.
Flexibility to adapt
The manufacturing industry is in constant flux with new technologies, market demand, fluctuating sector conditions, new products and machinery. Maintaining cash reserves allows you to respond quickly to new market needs through innovation and iteration, and increased ability in upgrading and pivoting your offerings.
Improved cash flow
Combining cost cuts with waste limiting processes frees up more working capital for productive re-investment back into your operations through strategic improvements and opportunities.
Potential Downsides of Inventory Reduction
Of course, over-stocking is a natural reaction to risk aversion. 74% of businesses have experienced longer lead times and shipment delays according to recent Capgemini data so the temptation to overload with inventory is a very real one. Minimising stock levels does present various danger factors, such as:
Supplier reliance
Just-in-Time practices depend on reliable, timely material deliveries. Be certain partnerships can fulfill commitments, and your supply chain is agile enough to counter geopolitical instabilities, supply delivery failure and delay, or you may miss production targets.
Higher unit costs
Smaller orders may lose volume discounts, but larger orders may become obsolete or outdated. Get it right so savings don't outweigh increased material expenses or create stoppages in production.
Meeting customer demand
Lean inventories leave little slack for changes in plans and conditions, so accurate forecasts and consistent supply chains are critical to avoid stock-outs and protect your reputation and guard your assembly line efficiency. Supplier audits can mitigate these factors.
Overall, the advantages will outweigh limitations if properly planned and managed. Data, collaboration and process optimisation ensure your reduced inventory strategy supports customer fulfillment and manufacturing operations.
Main Causes of Excess Inventory and Over-Stocking
Excess inventory is a common challenge in the manufacturing sector, particularly within OEM manufacturing, where the balance between supply and demand is critical. Several factors contribute to over-stocking, each with its complexities and implications for the supply chain. Understanding these causes is the first step toward developing effective strategies to mitigate their impact.
Here, we outline the primary reasons behind excess inventory, acknowledge the intricacies of supply chain management, and offer insights into proactive inventory control.
Forecasting Errors
Inaccurate demand forecasting is a leading cause of excess inventory. Overestimating customer demand leads to surplus stock, whereas underestimating can result in lost sales opportunities. Advanced predictive analytics tools can enhance forecast accuracy, yet even with sophisticated technology, market volatility can make precise forecasting challenging. According to an Inbound Logistics survey, a whopping 63% of businesses don't use technology to monitor supply chain performance (make sure you work with a logistics and warehousing partner that does!).
Inventory Management Inefficiencies
Lack of effective inventory management practices, such as failure to implement JIT (Just-In-Time) inventory systems or inadequate use of inventory management software, can result in excessive stock levels. Streamlining these processes through technology and strategic planning is crucial for maintaining optimal inventory levels.
Supplier Issues
Dependency on suppliers and their lead times can cause inventory build-up, especially if suppliers are unreliable or if there's a lack of effective communication and coordination. Establishing strong supplier relationships and diversifying supply sources can help mitigate this issue.
Changes in Demand
Shifts in market demand, whether sudden increases due to trends or decreases because of market saturation or real-world events, can lead to inventory mismatches. Continuous market analysis and flexible inventory strategies are essential to adapt to these changes.
Promotions and Discounts
Sales promotions and discounts can lead to temporary spikes in demand, causing companies to overstock. While these marketing strategies can boost sales, they require careful planning to avoid subsequent inventory surplus. Of course, this is less likely in the OEM sphere, but other psychologic factors can have an impact (market exuberance, currency fluctuation, etc).
Product Life Cycle
As products move through their life cycle stages, demand varies, leading to potential over-stocking of mature or declining products. Effective product life cycle management and strategic planning can help align inventory levels with product demand.
Economic Factors
Economic downturns or booms can significantly impact consumer purchasing behaviour, leading to excess inventory or stock shortages. Companies must stay informed about economic trends and adjust their inventory strategies accordingly.
Quality Issues
Defective products or quality control failures can lead to stock accumulation, as items need to be replaced or repaired. Implementing stringent quality control measures can prevent such issues and reduce unnecessary inventory buildup.
Lack of Communication
Poor communication within the company or with suppliers and customers can lead to misalignment of inventory levels. Effective communication channels and collaborative planning are vital for synchronised inventory management.
Bulk Ordering
We've touched on this before, but bulk ordering to unlock volume discounts or to hedge against supply disruptions is a common demon that can result in overstocking. While bulk purchasing can be cost-effective, it requires a delicate balance to avoid excessive inventory accumulation.
In the context of OEM manufacturing operations, these factors are particularly relevant given the industry's emphasis on efficiency and lean operations. There's a significant opportunity for cost savings through improved inventory management that manufacturer's shouldn't leave on the table. Addressing these causes through strategic planning and effective management practices is essential for optimising inventory levels and maintaining a competitive edge in the marketplace.
Consequences of Excess Inventory in the Manufacturing Sector
Excess inventory carries significant consequences that ripple through various aspects of a manufacturing operation, impacting profitability, efficiency, and relationships. For an OEM's procurement department, understanding these implications is crucial for informed decision-making and strategic inventory management. So what are the key consequences of over-stocking, and what are the priorities and challenges to be faced?
Storage Costs
Increased inventory levels directly translate to higher storage costs. Warehousing involves not just the physical space but also the utilities, security, and personnel required to manage the stock. Efficient inventory management minimises these expenses, contributing to overall cost reduction. If you outsource your warehousing to a logistics expert (and we argue you definitely should be doing this to unlock expert benefits) do a thorough audit of facilities, technology and working practices (more on checklist to do this here).
Carrying Costs
Beyond storage, carrying costs include insurance, taxes, and the capital tied up in inventory that could be otherwise invested. High carrying costs erode the bottom line, making effective inventory reduction strategies essential for financial health. Creating efficient warehousing and logistics operations with the help of a supply chain partner will minimise these.
Obsolete or Outdated Products
Technological advancements and changing market preferences can quickly render products obsolete, especially in the world of high value OEM manufacturing. Excess inventory of such products represents not just a financial loss but also an opportunity cost, as resources could have been used more productively elsewhere.
Reduced Cash Flow
Cash tied up in unsold inventory restricts a company's ability to invest in growth opportunities, R&D, or respond to market changes. Enhanced inventory management frees up cash flow, enabling more agile and responsive business operations.
Discounting and Loss of Profit Margins
To clear excess stock, companies often resort to discounting, which can significantly erode profit margins. While occasional promotions are effective, habitual discounting to manage inventory levels can undermine the brand's value proposition. Excess specialist components may not able to be sold off or easily find willing buyers.
Decreased Efficiency
Excess inventory can lead to cluttered warehouses and disorganised stock, making it harder to access necessary components. This inefficiency can slow down production processes and increase operational costs. Complex manufacturing processes usually go hand-in-hand with a myriad of SKUs and many components. In-house warehousing is not usually a manufacturing focus so eyes can be taken off balls. Better to utilise an expert outsourced facility and service if you don't have the skills or resource to invest in this area.
Increased Holding Time
The longer inventory sits unsold, the higher the risk of it becoming obsolete, damaged, or less desirable. This increased holding time can lead to financial losses and missed opportunities to invest in more profitable ventures.
Strain on Supplier Relationships
Over-stocking can strain relationships with suppliers, especially if it leads to inconsistent ordering patterns or delayed payments. Maintaining healthy supplier relationships is critical for supply chain resilience and operational efficiency. Using a master supplier can mitigate many of these issues, as they take responsibility for a more effective, agile supply chain network.
Write-off Risk
Inventory that cannot be sold due to obsolescence or damage must be written off, directly impacting financial statements and investor perceptions. Regular inventory reviews and proactive management can minimise this risk.
Customer Dissatisfaction
Finally, excess inventory can indirectly lead to client dissatisfaction. Resources spent on managing overstock could have been invested in improving product quality, customer service, or innovation, factors that would directly benefit the end client.
In the context of OEM manufacturing, these consequences underscore the importance of strategic inventory management aligned with lean manufacturing principles. Addressing these issues not only improves operational efficiency but also enhances competitiveness in dynamic market conditions.
Effective inventory management strategies, services such as Vendor Managed Inventory (VMI) and collaboration with a trusted 3PL provider, can mitigate these risks, ensuring that the company remains agile and responsive to market demands while also maintaining healthy profit margins and bolstering customer satisfaction.
In our follow-up article we will look at the full range of strategies to prevent excess inventory and over-stocking: Supply chain strategies to prevent overstocking.
Learn more about our OEM warehousing expertise
Acorn work with OEMs (including UK critical manufacturers) to offer outsourced warehousing to effectively and efficiently manage inventory for our clients.
We specialise in providing supply chain logistics services with warehousing and inventory management expertise.