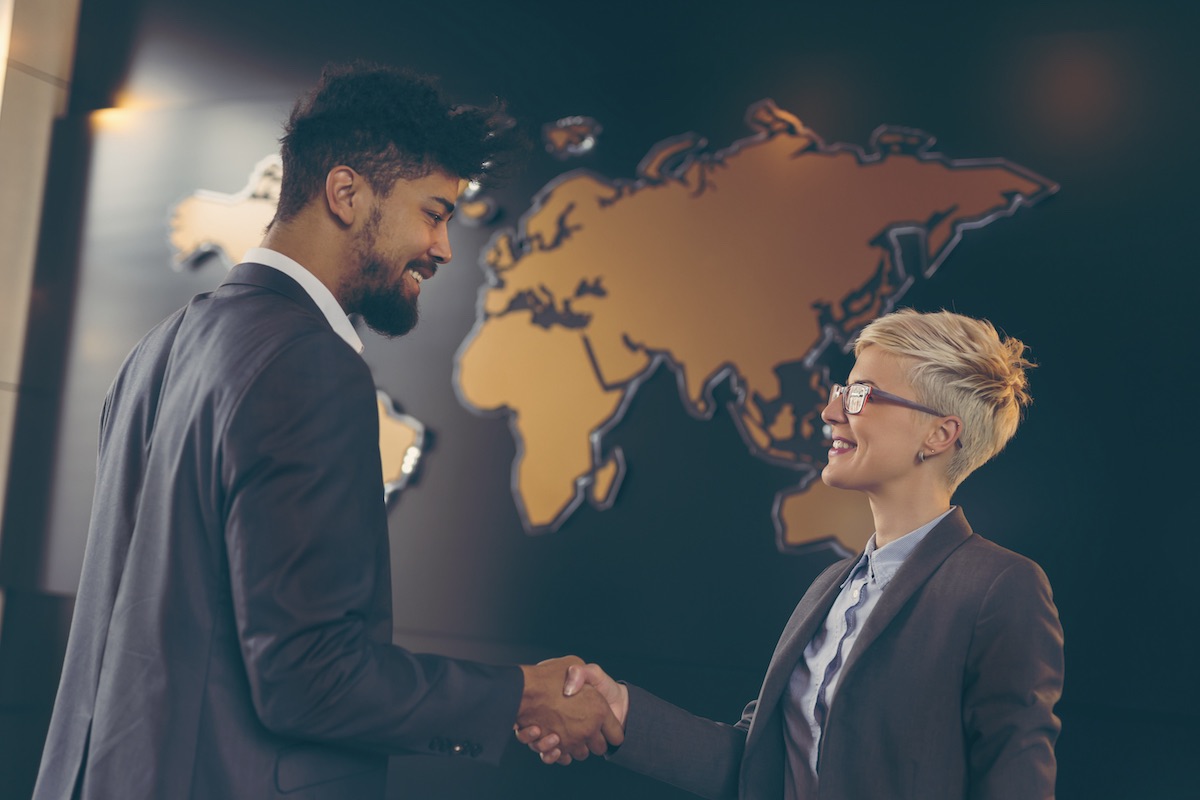
The global supply chain situation is changing rapidly. 'Rightshoring' manufacturing tailored to the ushering in of a new regional emphasis on local markets—after a historic period of free-flowing international global trade—is top of the economic agenda. A new supply chain reality is dawning and manufacturers need to be more flexible and agile in this new trading environment to adapt to these fresh economic winds.
Business as usual this is not. With a second term Trump presidency and a pivot to American exceptionalism/isolationism, Europe and the rest of the world are facing disruptive geopolitical shifts and dynamic changes in market forces. The COVID-19 pandemic illustrated how manufacturing networks can quickly adapt, how deftly they could create more supply chain agility against unpredictable events, and how swiftly resilience can be grown in logistics functions to mitigate the effects of unexpected supply/demand event shocks. These disruptions are not without precedents.
The UK's OEM manufacturers must step up to the challenge once again, leveraging all the skills recently shown, as the world trade order is undergoing a profound shift. Those who change and respond to this fragmented trade order, re-orienting around regional hubs, digitally transparent value chains and strategically diversified supply networks, will be set to gain a competitive edge moving forward.
More than 90% of manufacturing executives are prioritising regional supply chain strategies.
— Beyond Cost: Country Readiness for Manufacturing and Supply Chains, WEF Report 2025
Transitioning from global free trade to regional hubs
Nearly €4.5 billion of trade is made between the EU and the US every day. That trade is fairly balanced as the two giant trading hubs have relied on each other for goods, services and manufacturing — and have developed an intertwined and symbiotic trading relationship in the post-World War era — as global free trade has turbocharged the world economy. With the potential tariffs and cascading implications of a series of trade wars by countries around the world initiated by the ongoing fallout and decisions of the Trump administration, internal trade within regions is set to dramatically increase to the detriment of this pan-global supply and trade flow. The €1 billion/day flow between the EU and China could also rapidly evolve, especially if the US tariff system creates a divergence in economic gravity between major trading regions.
Britain has a high 66% of trade openness (trade-to-GDP ratio), like much of Western Europe (compare this to 27% of the US economy, and 37% for China). Europe and the UK thrive on international trade and don't have the same economies of scale or size advantages for internal market activity. It is within this environment why more than 90% of manufacturing executives are prioritising regional supply chain strategies, according to the World Economic Forum report, Beyond Cost: Country Readiness for Manufacturing and Supply Chains.
A strategic pivot is taking place for Europe to ensure manufacturing self-sufficiency in key sectors and industries (particularly energy and defence). It is an open questions where this leaves a post-Brexit UK which was geared according to its supporters for renegotiating free trade with the US, China and other global players after turning its head outside and away from the EU single market. These haven't materialised since implementation, and in the new regionalist reality look even further from magically happening. But still, as a significant economy within the G7, with key manufacturing, industrial, technological and service strengths, the UK has options within this fragmenting order, and potentially as a bridge between trade blocs, or more likely and obviously with a reassertion of direction toward close neighbours.
The rise of rightshoring and the power-of-two
60% state they are fundamentally restructuring their supply chains in the light of tariff uncertainty and changing trade certainties (this according to a 2025 State of Supply Chain Relex/Researchgate report). Supplier diversification, process automation and supply chain resilience strategies are being pursued in response to this increased market volatility. Companies are optimising cost structures, leveraging predictive analytics and proactive demand forecasting, while broadening their sourcing and supply networks (often leveraging expert logistics partners to manage this process for them — hint: this is our specialty focus for OEMs here at Acorn). Furthermore, deeply integrated supplier partnerships are 20% likelier to deliver stable operations during volatile market periods according to Supplier Relationship Management research by PwC.
The decoupling of intra-national supply chains is beginning to happen to some extent, but global trade and component supply is too complicated to unwind fully (and strategically not optimal). Instead supply chains are being shortened, diversified and optimised for resilience. The key trend is that of hedging against disruption and geo-political changes. 63% of manufacturers are employing a "power-of-two" geographical approach, and moving to source a majority of direct spending from two separate regions, thereby mitigating against regional trade and supply disruptions.
Onshoring and nearshoring strategies have been seen as the obvious and more bulletproof ways to bypass supply chain risk almost altogether, radically shortening supply chains to local alternatives, but in practice local materials production, regional capabilities and component expertise along with scale and sourcing advantages in certain localities makes it cost-inefficient, or simply impossible to replace these factors at a local or national level. Instead prudent diversification is the alternative.
Rightshoring looks at the optimal mix of manufacturing capability and facilities for every operation. It involves selecting optimal geographic locations for specific business processes, risk management and regulatory compliance allowing best operational performance alongside strategically optimal production goals. While onshoring can simplify regulatory compliance, bypass tariff issues, improve quality control and responsiveness, OEM manufacturing often needs complex componentry and assembly which requires a more hybrid approach that also takes in nearshoring and offshoring alongside native manufacturing.
Offshoring to distant countries may still be necessary for hard-to-replace sourcing, but the trend to nearshoring within regional trading zones is becoming a necessity for risk management and resilient manufacturing. It offers a balanced approach in a more volatile economic and geo-political environment. 90% of manufacturers who reshore have a positive experience, with 24% seeing cost reductions and 26% benefitiing from enhanced security of delivery (Source: Medius). These strategies also result in the enhancement of European Value Chains and regional security, resilience, and industrial sovereignty.
Objectives for better supply relationship management
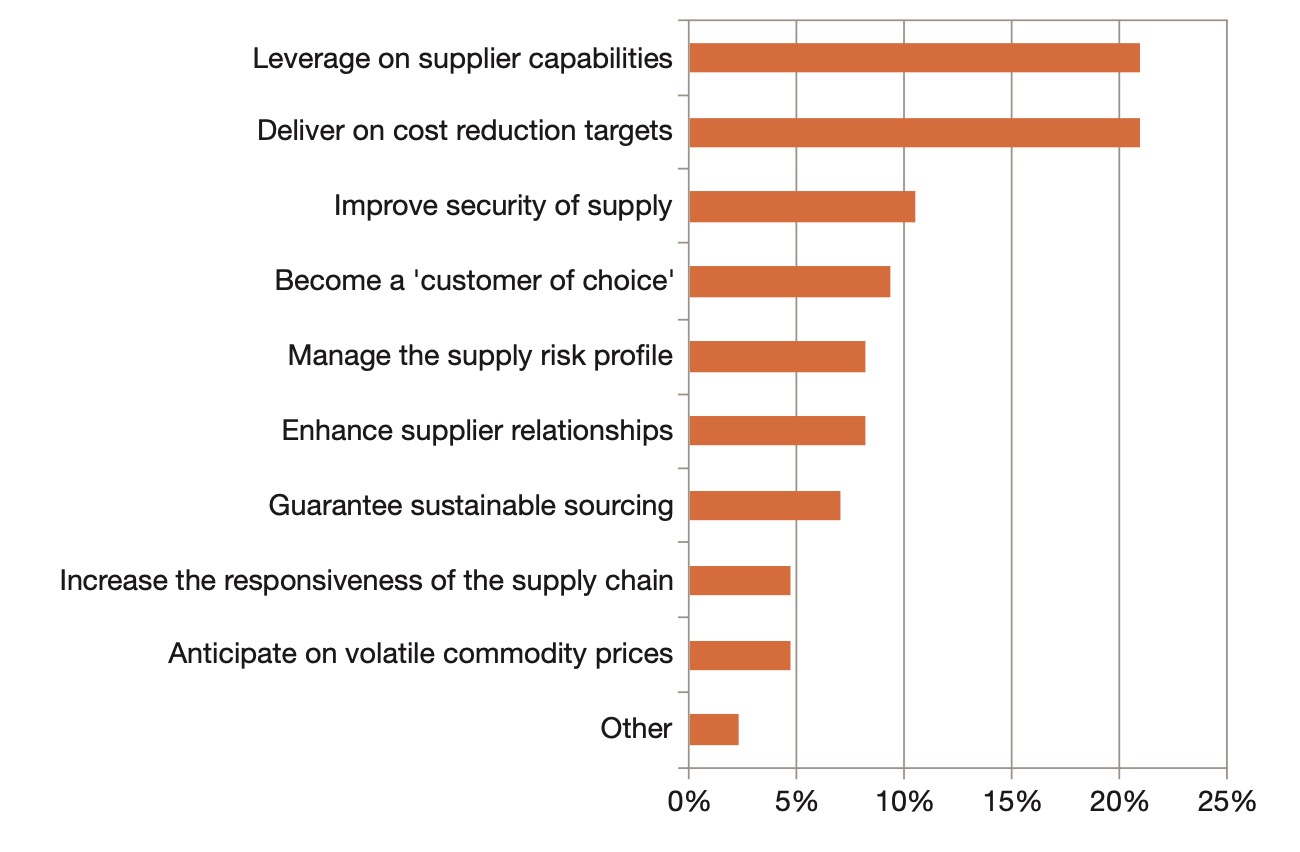
Source: PwC
All these developing strategies highlight the daunting task OEM manufacturers with complex componentry and materials needs have as the global supply chain and trade winds undergo a phase change. It shows how vital a dynamic and robust supplier network, and the logistics expertise to go with it, is. It is essential companies have reliable, timely supply, and to invest and work with the right logistics partners to achieve inventory security and efficiency. A report by Pwc on Supplier Relationship Management (see chart above), illustrates how key supplier relationships drive competitive advantage, and what the top objectives for using supply partners are.
The regulatory and geo-political headwinds are strengthening the pull of rightshoring strategies. While America may be pulling up the barriers, the reaction from Europe and Germany in particular (as it legislates to forgo the constitutional debt break and spend big on infrastructure and rearmament) presages a new European growth model and a big boost in regional demand. This will help insulate it from global trade wars, and is totemic of the new regionalism.
For UK manufacturers balancing compliance with EU standards, together with fostering SME innovation and access to the regional market, is more important that ever. Especially as heavyweights such as China now see their materials and own manufacturing supply base as economic weapons to wield within this new phase of global trade to combat a tariff-chaotic environment.
Rightshoring and regional supply chain reorientation represents more than a temporary shift, or a glitch in national relationships. It represents a fundamental restructuring and evolution in global manufacturing networks. Geopolitical events are reshaping trade patterns. UK manufacturers must embrace a hybrid approach balancing local production, regional partnership, and strategic global sourcing. A new emphasis on building dynamic supply chain networks and optimal supplier relationship management can turn these challenges into opportunities for OEMs willing to embrace these market developments, and step up their logistics game.
Sources: — Beyond Cost: Country Readiness for the Future of Manufacturing and Supply Chains, WEF/Kearney, December 2024 — Advanced Manufacturing: Building Resilient Value Chains, WEF/ETH Zurich – What the End of the Post-WW2 Order Means for Manufacturing, Manufacturing Digital, March 2024 — RELEX State of Supply Chain 2025, March 2025 — Xi Jinping swings his "assassin’s mace" of economic warfare, The Economist, February 2025 — Supplier Relationship Management: How key suppliers drive your company’s competitive advantage, PwC
Elevate your inventory management
Acorn work with companies to strengthen their logistics and diversify and derisk their supply chain.
In a new reality of more complex supply chain challenges, explore the services that can help you expand your logistics capabilities, and the benefits of working with an expert logistics partner.