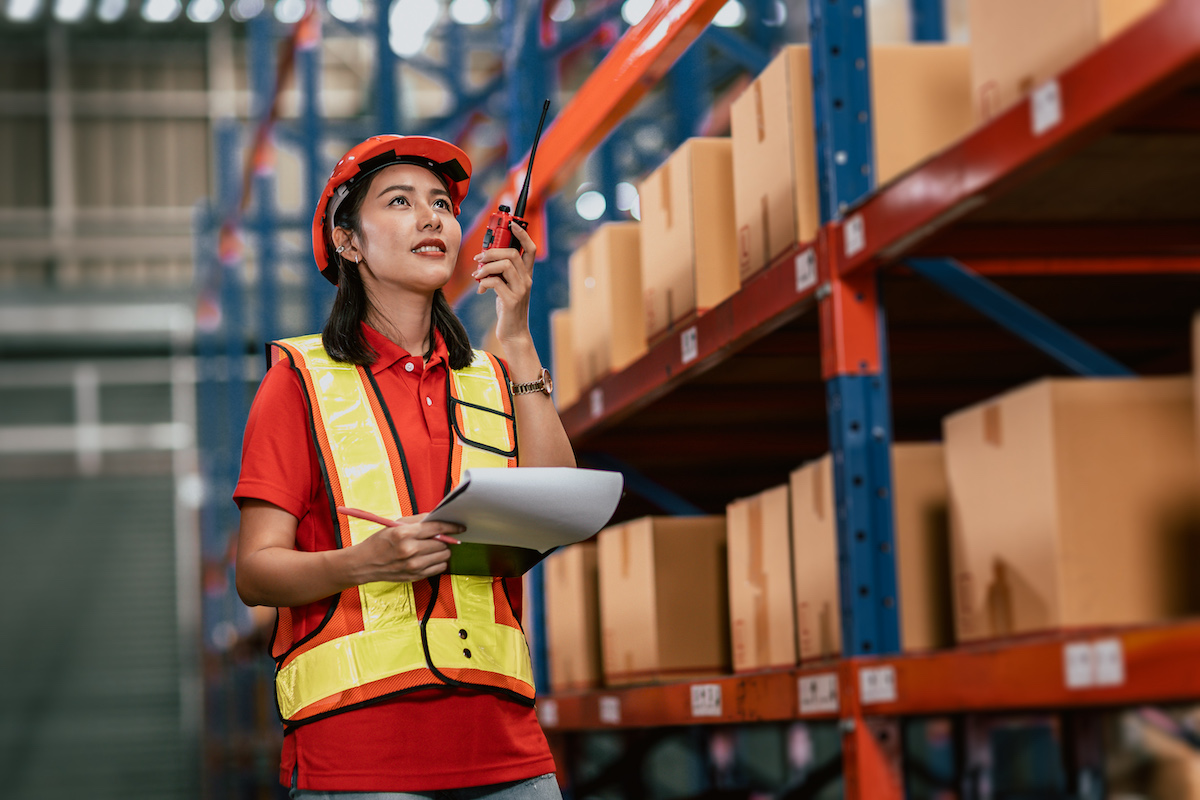
The modern warehouse is the foundation to any OEM supply chain, placed as it is between upstream procurement, and efficient downstream service and delivery to the production line and assembly. OEMs naturally focus on their core business as manufacturers of complex products. Therefore, warehousing and related supply chain logistics can often be seen, if not as an afterthought, then a poor secondary focus.
 
This would be a mistake.
Key competitive advantages can be had by focussing on the warehousing and related supply chain. This is especially true if these are joined with the manufacturing process (such as with DfA — Design for Assembly) and other logistics services to improve procurement, delivery and inventory management.
An outsourced warehouse with the right proactive supply chain partner to operate and execute these operations, will accelerate and up-level operational performance. While every company has unique needs and how you configure your warehousing will depend on a strategic plan, common elements for best practice and productivity are evident.
Whether outsourced, internal or some hybrid, these factors affecting warehousing need to be closely monitored, and will have a direct impact on supply chain and manufacturing performance:
 
The Seven Deadly Sins: — Inadequate Preventative Maintenance — Sub-optimal Facility Layout and Optimised Picking Paths — Outmoded Processes & Future Planning — Bad Health, Safety, and Sustainability — Excess Inventory & Poor Accuracy — Poor Housekeeping, Staff Development and Training — Under-utilisation and Integration of Services
Warehouse pitfalls and mistakes
An overview of these why we're looking at these 'sins':
Preventative Maintenance along with Facilities Layout and Picking Paths have a direct impact on operational efficiencies and may have been woefully overlooked in legacy facilities.
If processes are not updated with sufficient advance planning and process updates in place waste and cost inefficiencies begin to pile up compared to the savings achieved through modern methods.
For legal compliance and good modern business practice, health, safety and sustainable practices must be adhered to and put in place.
If inventory is inaccurate or bloated it can affect performance for deliverables to the production line and efficient usage.
Poor housekeeping with an unkempt, unclean warehouse affects morale, efficient use, and speaks to staff professionalism, training and morale (development and training are antidotes to this, while also enhancing all service levels).
Ultimately, if an OEM is not using value-added services to enhance warehouse logistics and supply capabilities, they are missing out on key differentiators and enhancements to their supply chain.
Let's take a closer look at each of these 'sins' and pitfalls to guarded against in more detail.
The First Deadly Sin: Inadequate Preventative Maintenance
If you want to ensure serious negative operational or financial impacts then not servicing, maintaining or upgrading systems and equipment is a sure fire way to do this. These issues disrupt workflow and slow down operations. Breakdowns are a lot more expensive to rectify than scheduled maintenance and servicing, where productivity can be managed and impacts mitigated so service levels are managed proactively.
Keeping a warehouse operating efficiently is both a skill and an art, that must be actively monitored and honed to get the most out of the facility for the specific use case and organisational need. A poorly maintained space and materials handling equipment (MHE) can have a domino effect that can extend outside the warehouse. Picking and packing, along with receiving/shipping delays due to MHE or WMS (warehouse management system) malfunctions or inefficiencies, can impact delivery schedules and inventory accuracy. Picking and Tracking may be affected by barcode scanning issues or tablet recording equipment glitches. On-time delivery performance may suffer.
The Second Deadly Sin: Sub-optimal Facility Layout and Optimised Picking Paths
A badly planned warehouse facility limits the growth of a business, and many manufacturers do not have an optimal level of in-house expertise (that's why we think leveraging the expertise of an outsourced warehousing specialist is the best option for many OEMs). To maximise performance, you need the right amount of space configured in the best possible way. This is mission critical for organisations to pursue and achieve a lean manufacturing strategy.
OEMs often have complex procurement requirements and/or have many parts for later assembly in downstream complicated manufacturing process. Managing multiple SKUs (along with their lifespan and ideal buffer quantities) so they are stored and then conveyed to production line efficiently requires well oiled procedures and bedded-in expert handling, sequencing, and facilities storage.
Sub-optimal routes have direct implications for delivery efficiency, goods-in, pick and pack times, potential staff safety risks, accuracy and tracking for maximal facility workflow.
Poorly executed or deficient layout and handling facilities can lead to additional handling and storage costs and an increased likelihood of loss or damage due to excessive handling or recovery.
The Third Deadly Sin: Outmoded Processes & Future Planning
Still relying on manual practices and paperwork? This is a major red-flag for your operations. A modern fit-for-purpose warehouse requires a modern warehouse management system and integrated technologies. In-house and legacy facilities will either not want to go through the upheaval of the transformation, may what to transform but not have the same level of expertise as a specialist provider, or simply wish to delay investment and change for various business and management reasons.
An outsourced warehouse specialist focuses on transforming, modernising and improving relevant processes as a core service. Regular upgrade and continued integration of additional technological capabilities and tools is essential to improve relative to market demands and improve modern supply chain function. Mistakes and inefficiencies are eliminated through a data-driven, realtime tracking system. Additional strategic planning can address your warehousing relative to sector competitiveness, plan for expansion, order scheduling and new product lines. Staffing shortages in this area must also be mitigated against if you have juggling all these balls in-house.
Failures to invest and plan in this area exposes OEMs open to market threats, competitive disadvantage, and strategic weaknesses that limit their operational capabilities.
The Fourth Deadly Sin: Bad Health, Safety, and Sustainability
Neglect health and safety procedures, and sustainable business practices and you have a bad underperforming business. Instances of workplace injury increase markedly if safety isn't built into the working warehouse environment and personnel aren't properly trained with the relevant skills.
Within the layout, spacing, lighting, and signage are important factors. Preventative maintenance and good housekeeping — keeping a clean, ordered environment — as mentioned elsewhere in this article are also highly relevant factors. Lax controls and materials safety also impacts equipment, facilities, component and product quality over and above the human element. By addressing personnel health and safety you not only prevent injury but ultimately get a more productive, positive and healthy work environment. This has obvious performance benefits.
Reducing environmental impacts through waste management, sustainable packaging and procurement, efficient energy and materials usage helps satisfy regulations, social responsibility, and can have a positive impact on costs (efficiency and regulatory savings).
At Acorn we are already providing sustainable packaging solutions to clients, and have exacting environmental standards (including ISO14001, partnering with ecologi for positive carbon solutions, and are continuing to implement practical positive environmental actions in our warehouse facilities and wider supply chain logistics services).
The Fifth Deadly Sin: Excess Inventory & Poor Accuracy
Unwanted or excessive stock is the cardinal sin in good inventory management. Yet OEMs do it all the time. Sometimes for convenience, sometimes because it is a minimum order quantity, or because they aren't sure how much stock they have due to inaccurate tracking. It can be easier to add a buffer to be safe rather than suffer a stock-out. It is easy and understandable why overworked procurement departments may do this. However inaccurate and suboptimal inventory levels incur significant costs for OEMs that can be mitigated by professional warehouse operations.
Reducing stock levels is a direct route to a leaner supply chain, but this must also be married to correct demand planning alongside the urgencies and needs of an agile resilient supply chain in a world where more disruption and shortages abound. There's been a clear change in difficulty managing this in recent times (COVID, lockdowns, supply shortages and shipping delays, port congestion embargo's). Managing this internally may require more resources being put into the procurement and warehouse functions. And it puts more onus on modern warehouse facilities with well integrated warehouse management systems, to function effectively. Using an outsourced warehouse partner (especially if they have additional supply chain network expertise) can solve these needs most easily.
The Sixth Deadly Sin: Poor Housekeeping, Staff Development and Training
Fail to fully activate a supply chain network from its storage and distribution fulcrum in the warehouse, and a company can fail to build crucial competitive advantages and supply chain synergies. Comprehensively integrating supply chain assets and solutions through a supply chain partner who is overseeing an outsourced warehouse fosters agility and competitive advantages crucial for OEMs.
Vendor managed inventory (including reaching out from warehouse to point-of-assembly) can integrate and optimise just-in-time supply to immediate production line needs, increasing agility and efficiency, relieving storage and order fulfilment burdens internally. Kitting and box build work in a warehouse facility with quality-assured assembly facilities can provide pre-tested modular components for seamless production line integration. Components procurement alongside storage and delivery services can aid in more efficient data-driven inventory planning. Aftermarket provision can alleviate logistics burdens while unlocking a valuable revenue driver and contributing to product and lifecycle sustainability. All or a combination of these can be implemented in a bundled 3PL service that promotes responsiveness and provides maximum coordination and improved resilience to supply chain demands.
Close attention must be paid to all these aforementioned elements — people, processes, technology and environment — to alleviate and turn these deadly sins into operational wins. A solid warehouse function is needed to build, continuously improve and refine performance and operational capability. Improvement initiatives are essential not optional in the context of the much overlooked warehouse. Hence why an outsourced solution, ceding responsibility, control and expertise to a trusted partner is a winning strategy.
The Seventh Deadly Sin: Under-utilisation and Integration of Services
Fail to fully activate a supply chain network from its storage and distribution fulcrum in the warehouse, and a company can fail to build crucial competitive advantages and supply chain synergies. Comprehensively integrating supply chain assets and solutions through a supply chain partner who is overseeing an outsourced warehouse fosters agility and competitive advantages crucial for OEMs.
Vendor managed inventory (including reaching out from warehouse to point-of-assembly) can integrate and optimise just-in-time supply to immediate production line needs, increasing agility and efficiency, relieving storage and order fulfilment burdens internally. Kitting and box build work in a warehouse facility with quality-assured assembly facilities can provide pre-tested modular components for seamless production line integration. Components procurement alongside storage and delivery services can aid in more efficient data-driven inventory planning. Aftermarket provision can alleviate logistics burdens while unlocking a valuable revenue driver and contributing to product and lifecycle sustainability. All or a combination of these can be implemented in a bundled 3PL service that promotes responsiveness and provides maximum coordination and improved resilience to supply chain demands.
Close attention must be paid to all these aforementioned elements — people, processes, technology and environment — to alleviate and turn these deadly sins into operational wins. A solid warehouse function is needed to build, continuously improve and refine performance and operational capability. Improvement initiatives are essential not optional in the context of the much overlooked warehouse. Hence why an outsourced solution, ceding responsibility, control and expertise to a trusted partner is a winning strategy.
Getting the Most Out of Outsourcing your Warehousing
While we've outlined key pitfalls and what to avoid in OEM warehousing, it is important to not lose sight and ultimate focus on the fact enhancing all these 'sins' will create tremendous positive improvement in operations.
When outsourcing your OEM warehouse function, keep the following success factors at the fore to foster harmony, efficiency and a fruitful collaboration with your logistics provider:
Communications and KPIs
Any outsourced warehouse partnership requires reliable and efficient communication channels, with the scope to operate autonomously to meet defined KPIs according to client needs. Progress should be tracked against agreed KPIs and deliverables, with appropriate levels of transparency. Order fulfilment, delivery-on-time and inventory turns should be measured and optimised.
Ordering and Data Integration
Integration of digital ordering and inventory control through an efficient warehouse management system is foundational for achieving smooth operations, order fuilfilment from receipt to delivery, and to extract efficiencies in inventory, ordering and planning through data analysis.
Delivery and Integration
To maximise delivery efficiency, coordination between the warehouse, transportation, and the client facility is paramount. Using EDI and automated tracking facilitates visibility and assurance in the delivery of accurate inventory shipments. Close cooperation in logistics eliminates delays and errors from the process.
Learn more about our OEM warehousing expertise
Acorn work with OEMs (including UK critical manufacturers) to offer outsourced warehousing to effectively and efficiently manage inventory for our clients.
We specialise in providing supply chain logistics services with warehousing and inventory management expertise.