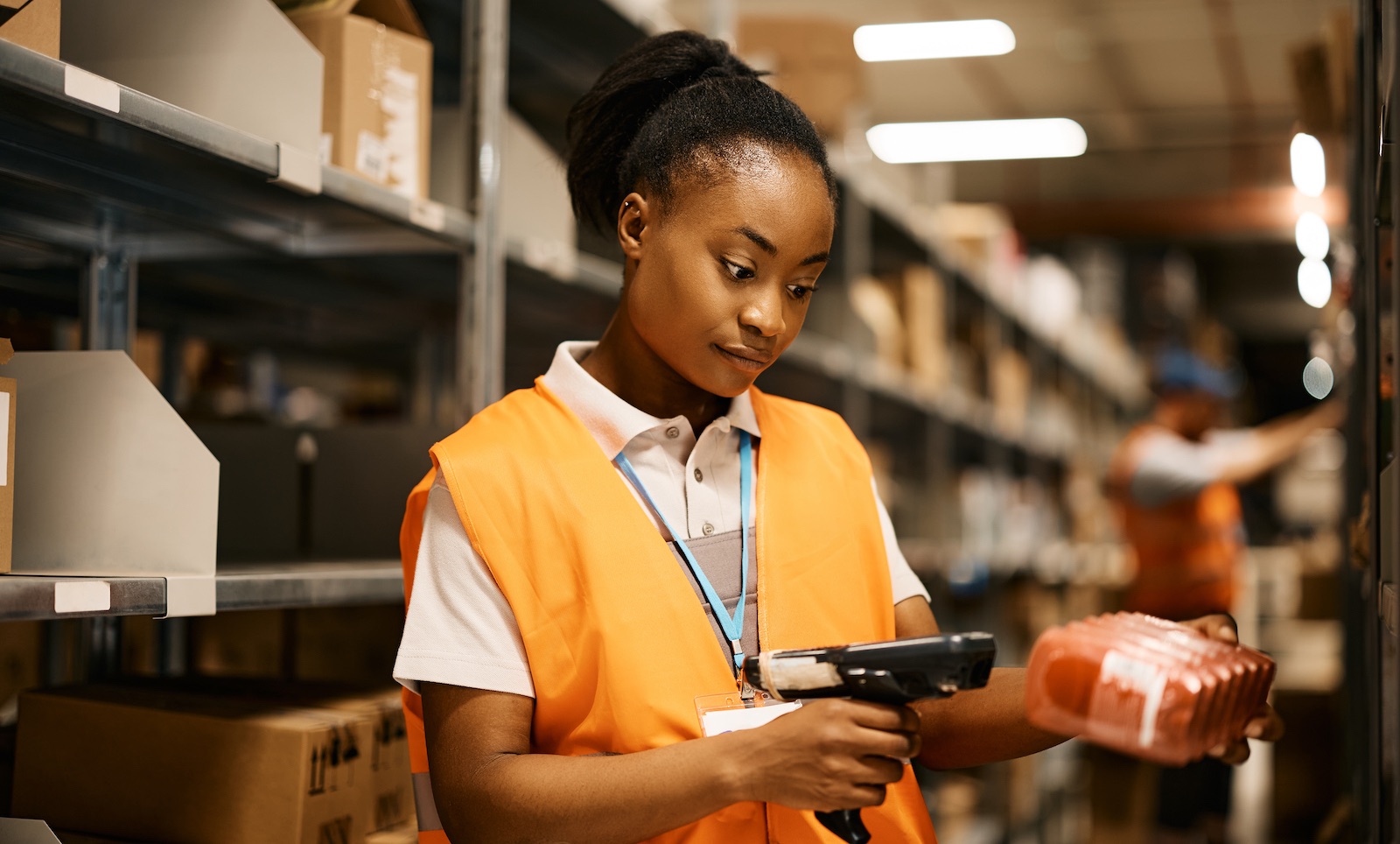
The worlds of manufacturing logistics, warehousing, and supply chain management can be pretty complex. These areas are filled with all sorts of industry-specific terms and abbreviations that may appear overwhelming to those unacquainted with them.
[ Acronyms & abbreviations: jump to 0–9, A–G, H–N, O–Z ]
While these worlds are full of industry-specific jargon almost all this terminology exists to help facilitate efficient and rapid communication among specialists and industry professionals from the same field. Knowing these terms is especially crucial in the manufacturing logistics sector where fast communication and efficiency are keys to success.
From ABC (Activity Based Costing) to WMS (Warehouse Management System), this list of industry terms can help you communicate with your fellow professionals more proficiently, fill in any knowledge gaps, and stay up-to-date on the latest 3LAs ("three letter acronyms" for the uninitiated).
Check out the comprehensive list below to ace your acronyms, and see if you have mastered the language of logistics.
Acronyms for manufacturing logistics and supply chain
[ Logistics acronyms: jump to 0–9, A–G, H–N, O–Z ]
3PL — Third Party Logistics
What is 3PL in logistics?
3PL (Third Party Logistics) refers to the outsourcing elements of a company's inventory, distribution and fulfilment functions to a third party expert provider. Under this approach, manufacturers are responsible for their supply chain but outsource specific elements such as components supply, inventory management and storage, and transportation to a trusted supply chain partner.
4PL — Fourth Party Logistics
What is 4PL?
4PL (Fourth Party Logistics) refers to a lead logistics provider (LLP) that assembles resources, planning capabilities, and technology of both its own and other organisations to design, build and manage comprehensive supply chain solutions. First defined as a concept by Andersen Consulting.
5PL — Fifth Party Logistics
What is 5PL?
Fifth Party Logistics (5PL) differs from a 3PL or 4PL provider as it looks to focus on wider supply networks as opposed to individual supply chains. A 5PL logistics provider will oversee all supply chains within a client organisation, planning, organising and implementing all of a client's logistics functions.
5S — Sort, Straighten, Shine, Standardise, Sustain (Seiri, Seiton, Seisou, Seiketsu, Shitsuke)
What is 5S in logistics?
5S is a system for organising efficient, productive workplaces based on five key principles. The five elements of 5S are Sort, Straighten, Shine, Standardise, and Sustain. 5S has a focus on eliminating waste, improving workflow, and reducing the number of processes needed in production. 5S is considered foundational in TPM (Total Productive Maintenance), as an integral part of the Toyota Production System (TPS). 5S is often referred to as 5S Lean, or as 5S principles.
6S — Six Sigma
What is 6S?
Six Sigma (6σ or 6S) is a set of techniques and tools to improve manufacturing quality through process improvement, removing the causes of defects, and minimising variability in manufacturing. It is a data driven approach that provides statistical tools to eliminate manufacturing defects, and identify and reduce causes of error.
ABC — Activity Based Costing
What is ABC?
ABC (Activity Based Costing) is a costing methodology that identifies activities in an organisation and assigns the overhead costs and expenses of each activity (with the resources used for such activity) to all products and services according to the actual consumption of each.
AEO — Authorised Economic Operator
What is AEO status?
AEO (Authorised Economic Operator) status illustrates a company is competent in customs-related operations and part of the international supply chain. AEO status is based on internationally recognised quality standards and criteria. The two types of status are: Authorised Economic Operator Customs Simplification (AEOC), and Authorised Economic Operator Security and Safety (AEOS), which offer benefits for customs clearances and authorisations.
APS — Advanced Planning Systems or Advanced Planning and Scheduling
What is APS?
APS is a management process in manufacturing whereby raw materials and production capacity are optimally allocated to evolving levels of demand.
ATO — Assembled To Order
What is ATO?
ATO (Assembled To Order) is a strategy where constituent parts of products are already manufactured but not fully assembled. This business production strategy allows customisation and final assembly to order.
BOL — Bill of Lading or B/L
What is a BOL?
Originally used to refer to the carriage of cargo by sea, a BOL (Bill of Lading) now refers to any type of carriage of goods. A Bill of Lading is a document issued by a carrier granting a receipt of cargo for shipment, and provides proof of transport, proof of receipt and title of ownership.
BOM — Bill of Materials
What is a BOM?
BOM (Bill of Materials) generally refers to a structured list of materials, sub-assemblies, components, and parts, along with quantities of each. A manufacturing BOM (MBOM — manufacturing bill of materials) contains all parts and assemblies necessary for the complete manufacture of a product.
CAD — Computer-Aided Design
What is CAD?
Computer-Aided Design (CAD) simplifies the design of a product by digitising the process, allowing easier processing, alteration, and output workflows. CAD software increases design productivity, quality, documentation and communication.
CAM — Computer-Aided Manufacturing
What is CAM?
Computer-Aided Manufacturing (CAM) automates the manufacturing process by using software and computer-controlled machinery. It aims to make a more consistent process, with faster and more agile production, along with minimising materials and energy waste.
CEM — Contract Electronics Manufacturer
What is a CEM?
A CEM (Contract Electronics Manufacturer) is a company that makes and assembles products (partly and in full) under contract for an OEM.
CIF — Cost, Insurance and Freight
What does CIF stand for?
CIF (Cost, Insurance and Freight) refers to the expense to cover costs, insurance and freight against the possible loss or damage to the buyer's order while in transit, paid by the seller.
COGS — Costs of Goods Sold
What does the abbreviation COGS mean?
The acronym COGS (Costs of Goods Sold) refers to the direct costs of producing a goods sold by a firm, including the cost of materials and labour directly associated with production.
COQ - Cost of Quality
What is COQ?
Cost of Quality (COQ) is a methodology to determine the overall impact of product quality on business costs. Prevention (such as testing and audits) and appraisal costs (inspection and process controls) are proactive, preventative quality measures (CoGQ — Cost of Good Quality). Internal failures (component or product defects, remanufacturing), and external failures (replacement or repairs, shipping damage) are the costs of poor product manufacture and delivery (CoPQ — Cost of Poor Quality).
Cross-docking
What is cross-docking?
Cross-docking is a logistics practice where materials are unloaded from truck to dock, then directly loaded onto another truck.
DMAIC — Define, Measure, Analyse, Improve, Control
What is DMAIC?
DMAIC (Define, Measure, Analyse, Improve, Control) is a continuous improvement cycle and roadmap for Six Sigma (6S). It is an approach aimed at finishing projects in short timeframes as part of a lean manufacturing approach.
DFA — Design for Assembly
What is DFA in manufacturing?
Design for Assembly (DFA) focusses on the optimisation and simplification of the assembly process of a final product. It aims to make the production process faster, simpler and consistent through the reduction and simplification of assembly to make it more efficient.
DFM - Design for Manufacturing
What does DFM mean in manufacturing?
DFM (Design for Manufacturing) is a process where component parts, and production operations are designed for optimised manufacturing, usually through lowering complexity and the cost of materials. It merges the production and design processes to create higher quality products at lower cost by maximising ease of manufacture.
DFRL — Design for Reverse Logistics
What does DFRL mean?
Reverse logistics is the ability to accept returned items from customers. A supply chain operation following DRFL principles is designed for a smooth and logical returns process and aftermarket repair, upgrade and support.
EDI — Electronic Data Interchange
What is an EDI?
An EDI (Electronic Data Interchange) refers to a digital approach to document exchange in a standardised format that replaces traditional paper-based invoices and purchase orders. It facilitates inter-company communication and sharing of data.
EOQ — Economic Order Quantity
What is the meaning of EOQ in logistics?
EOQ (Economic Order Quantity) refers to a calculated amount that is the ideal order size. A concept sometimes referred to as the optimum lot size, it minimises excess inventory and holding costs, while allowing demand to be met without overspend.
ERP — Enterprise Resource Planning
What is ERP?
Enterprise Resource Planning (ERP) is a software system that facilitates the smooth running of core company functions. ERP connects key areas of business processes and supply chain management, including (but not limited to) finance, human resources, manufacturing, supply chain, and procurement.
FIFO — First In First Out
What is the meaning of FIFO?
FIFO (First In, First Out) is an inventory replenishment method where items that arrive first in a facility are also the first out. It prioritises the rotation of parts and minimises the need for unnecessary stock.
FLT — Forklift Truck
What does FLT stand for?
A specialised, highly manoeuvrable industrial truck used to lift and move materials short distances.
FMEA — Failure Mode and Effects Analysis
What is FMEA?
Failure Mode and Effects Analysis (FMEA) is an inductive method to studying defects in logistics processes, and an advanced approach to quality planning during product development.
FOB — Free On Board
What does FOB in logistics mean?
In shipping, FOB refers to a term in international commercial law specifying at what point obligations, costs and risk involved in delivery of goods shifts from seller to buyer (under the Incoterms standard published by the International Chamber of Commerce).
IBP — Integrated Business Planning
What is IBP?
A planning process that integrates across two or more business and enterprise functions to maximise financial value. It acts as a bridge between stategy and execution, extending the principles of Sales and Operational Planning (S&OP) throughout the value chain.
IIoT — Industrial Internet of Things
What is IIoT?
Industrial Internet of Things (IIoT) refers to the industrial application of network-enabled devices, sensors, instruments cloud computing, and other smart machinery. It is a subset of the IoT (Internet of Things), and includes M2M (Machine-to-Machine) communication. It allows for automated data collection, exchange, monitoring and analysis.
Incoterms
What does Incoterms mean in logistics?
Incoterms, or Itnernational Commercial Terms in full, are pre-defined commercial terms published by the ICC (International Chamber of Commerce) referring to international commercial law defining arrangement of shipments and liabilities.
ISA-95 (also ANSI/ISA-95) — International Society of Automation standard
What is ISA-95?
ANSI/ISA-95 is a standard for developing automated interfaces between enterprise and control systems, smart manufacturing and IIoT, with particularly relevance to the manufacturing industry. ISA-95 objectives aim to provide consistent terminology and standards for supplier-manufacturer communications
ISO — International Organization for Standardization
What is ISO?
ISO is an international standards organisation that develops and publishes international standards in technical and non-technical fields.
JIT — Just In Time
What is JIT?
JIT (Just In Time) is a management strategy aligning materials orders from suppliers directly with production schedules — as an inventory strategy to increase efficiency and decrease waste and inventory costs.
LIFO — Last In First Out
What does LIFO mean?
LIFO (Last In, First Out) is a common inventory alternative to first in, first out, LIFO assumes that the products created most recently will also be the first to be sold. This system allows older inventory costs to remain on balance sheets as more recent inventory costs are expensed promptly.
LLP — Lead Logistics Provider
What is an LLP?
Commonly, this is another way to refer to a fourth party logistics provider, a high level strategic supply chain and logistics partner.
LSP — Logistics Service Provider
What is an LSP?
An LSP (Logistics Service Provider) is a company provides logistics service such as transport, procurement, warehousing and inventory management as a commercial service to another company.
MES — Manufacturing Execution System
What is the meaning of MES?
A manufacturing execution system (MES) monitors, tracks, and controls an entire production lifecycle in real-time, optimising the manufacturing process and improving production output. A MES software platform can track and document the entire production process including production, quality, logistics and maintenance. It supports traceability of materials/components along with proof of processes and documentation, including for compliance and servicing.
M2M — Machine to Machine
What is M2M?
Machine to Machine (M2M) refers to point-to-point data flow and direct wired or cellular communications between mechanical and electronic devices without the use of the Internet. In an industrial context, M2M data communication can be between machine tools, robotics, sensors and information systems in the factory, warehouse or supply chain. M2M is an enabler of 4IR and the industrial Internet of Things (IoT).
MHE — Materials Handling Equipment
What is MHE?
MHE (Materials Handling Equipment) refers to mechanical equipment used for movement, storage, control and protection of materials, goods and products throughout the process of manufacturing, distribution, consumption and disposal. It encompasses a broad range of devices and systems, including conveyors and carousels, Automated Storage and Retrieval Systems (AS/RS), cranes and powered trolleys, forklift and reach trucks,
MOQ — Minimum Order Quantity
What does MOQ mean?
Minimum Order Quantity (MOQ) is the minimum number of items in an SKU a supplier will accept for an order.
MRO - Maintenance, Repair, and Operations
What is MRO in logistics?
MRO refers to the equipment, tools and other supplies and materials for the routine maintenance, repair and operations of a business. Examples of MRO items include consumable materials such as cleaning supplies, repair tools, personal protective equipment (PPE), and safety products. These inventory items, while not included in the direct cost of production are essential to the smooth and efficient running of production processes and company facilities. MRO is sometimes referred to as Maintenance, Repair and Overhaul.
MRP — Materials Resource Planning or Manufacturing Resource Planning
What is MRP?
An MRP (Materials Resource Planning) system is designed to help manufacturers in planning, production, scheduling and inventory control. Helps manufacturers balance supply and demand to ensure strategic scheduling and order placement.
NIFO — Next In First Out
What does NIFO mean?
Under the NIFO (Next In, First Out) inventory valuation method, an item’s cost is determined based on the replacement value, rather than relying on previously established expenses. This method is most helpful for companies looking to price ahead of inflation.
ODM — Original Design Manufacturer
What is an ODM?
An ODM (Original Design Manufacturer) builds a product from the original design specifications of another. Similar to a CEM, an ODM.typically owns the IP for the product themselves.
OEE - Overall Equipment Effectiveness
What is OEE?
Overall Equipment Effectiveness (OEE) measures manufacturing productivity, and is a measure of how well utilised are the facilities, time and material of a manufacturing operation. OEE is a commonly used KPI (Key Performance Indicator) in lean manufacturing.
OEM — Original Equipment Manufacturer
What is an OEM?
An OEM (Original Equipment Manufacturer) is any manufacturer that sells to a secondary company. It may design and market complete products for customers, or certain modules, components or sub-systems that are part of a more complex manufactured product. OEMs may outsource assembly and manufacture to concentrate on research, design, go-to-market strategy and services.
PLM — Product Lifecycle Management
What does PLM mean?
Product Lifecycle Management (PLM) is the strategic process for managing the entire lifecycle of a product from inception, concept and design, development, manufacture and launch, sales and servicing, through to disposal and end-of-life.
POD — Proof Of Delivery
What does POD stand for?
The method establishing contents have been received to a recipient by the sender. Usually taken in electronics form in modern logistics for better data tracking and realtime logistics and delivery information.
POE — Port of Entry
What is acronym, POE?
POE (Port of Entry) refers to the location where the product may lawfully enter the country (and pass through customs arrangements where necessary).
PPE — Personal Protective Equipment
What is PPE in logistics?
PPE refers to a class of personal protective equipment designed to be worn or used by an individual for protection in the workplace from health and safety hazards. PPE equipment can include safety helmets, masks and other respiratory protective equipment (RPE), eye protection, safety footwear, headwear and harnesses, along with high-visibility or protective clothing.
QA — Quality Assurance
What is QA?
A QA (Quality Assurance) process assures product quality is assessed and compared to specifications, ensuring minimum requirements are met.
RFID — Radio Frequency Identification Device
What is RFID?
RFID (Radio Frequency Identification Device) is a wireless data collection technology highly useful in logistics and inventory management for tracking. It can be used to tag and read everything from inventory to personnel. A RFID system comprises a scanning antenna, a transceiver and a transponder (antenna and transceiver are often combined into a scanning device). The transponder is often referred to an RFID tag or smart label.
RoHS — Restriction of Hazardous Substances
What is RoHS?
RoHS (Restriction of Hazardous Substances) is a European Union directive restricting the use of hazardous materials in the manufacture of various types of electronic and electrical equipment.
S&OP — Sales and Operational Planning
What is S&OP?
Sales and Operational Planning (S&OP) is an integrated business management process through which a company's executive team achieves focus, alignment and direction throughout all functions of the organisation.
SCM — Supply Chain Management
What is SCM?
The management of the flow of goods and services from point of origin to point of use/consumption. Involves the storage of raw materials, components, of work-in-progress inventory, and of finished goods.
SKU — Stock Keeping Unit
What is an SKU?
An SKU is a unique code or identifier referring to a specific stock unit by a company or vendor, and is used for identifying and tracking. SKU's can also be attached to intangible but billable products (such as units of repair, assembly, or QA processes).
TMS — Transport Management System
What is a TMS?
A Transport Management System is a specialised software system that helps companies manage the physical movement of goods as part of larger supply chain operations.
TPM — Total Productive Maintenance
What is TPM?
Total Productive Maintenance is a method of physical asset management focussed on maintaining and improving manufacturing machinery. TPM was developed by Seiichi Nakajima in Japan between 1950—1970.
TQM - Total Quality Management
What is the meaning of TQM?
TQM refers to the detection, reduction and elimination of errors in manufacturing and the supply chain, along with improving company outputs including products and services.
UPC — Universal Product Code
What is a UPC?
A Universal Product Code (UPC) is commonly used worldwide to track items in stores. The adoption and spread of UPC has significantly contributed to supply chain inventory tracking.
VMI — Vendor managed inventory
What does VMI mean?
VMI (Vendor Managed Inventory) is a common inventory management technique. In VMI, a logistics partner takes responsibility for the supply and management of goods for a client company. A VMI partner will manage inventory, stock levels, and fulfillment.
WH — Warehouse
What is WH?
WH is the abbreviation for warehouse, a commercial building for the efficient storage of goods. Modern warehousing generally integrates technologies, storage racking and other technologies for the safe and efficient storage and retrieval of items.
WIP — Work In Progress
What does WIP mean in logistics?
The term WIP (Work In Progress) describes the inventory of unfinished goods that have begun the manufacturing process but are not yet complete. WIP typically includes raw materials, partially completed products and packaging materials needed for production and distribution processes.
WMS — Warehouse Management System
What is the meaning of WMS?
WMS (Warehouse Management System) refers to the software and tools for warehouse administration and operations control of items from point of arrival to departure from the warehouse. May include functions for inventory management, fulfilment and returns, cross-docking, item location and replenishment. Warehouse Management Systems are often integrated or used alongside related items such as ERP, TMS and inventory management systems.
We hope you find this comprehensive list useful. Now you've brushed up on your supply chain jargon, why not check out our extensive product range of industrial components, or scope of our key supply chain services.