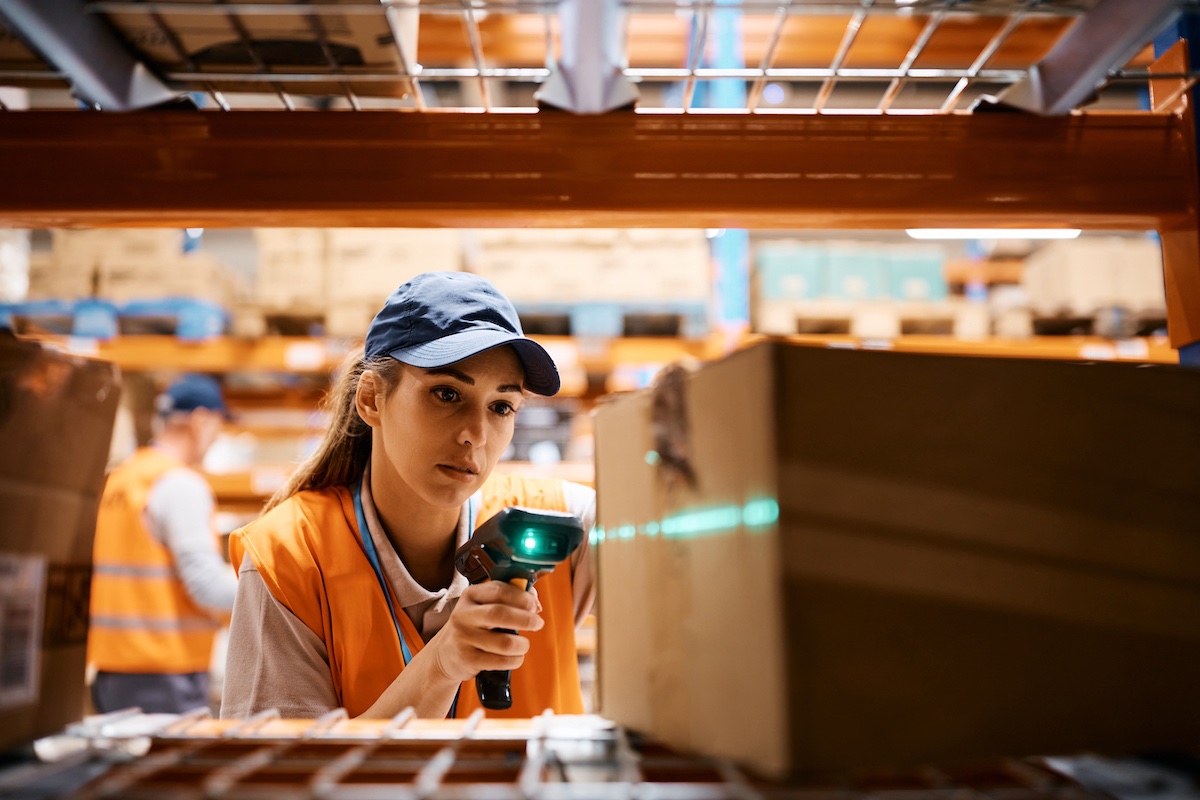
Warehouse optimisation is a process designed to address receiving, holding, and moving materials to the production line, along with all other aspects of product shipment, in an integrated and seamless way.
Issues such as inventory control, inefficient warehouse processes, and shipping delays can result in lost profits and dissatisfied customers, therefore improving overall warehouse performance is key to efficient and profitable manufacturing.
With a fully optimised warehouse, you can expect better results, a more streamlined operation, and peak performance.
Efficient handling, product flow, transportation and delivery are all crucial to a dynamic warehouse function. Our consultancy service helps you drive efficiencies in your manufacturing business by tuning the right mix of on-site vs off-site facilities in relation to inventory storage, while maximising current space vs warehouse consolidation and outsourcing.
Let's look at why warehouse optimisation is so important for a the modern OEM.
Why Warehouse Optimisation is Important
Warehouse optimisation is a crucial aspect of supply chain management that involves improving the efficiency and productivity of a warehouse. It is a process that encompasses the reorganisation of warehouse operations, layout, and processes to achieve maximum efficiency. Optimising your OEM warehousing can help you reduce costs, boost productivity, streamline operations, and enhance visibility.
Primary Benefits of Warehouse Optimisation
Improve Forecasting
Warehouse optimisation can help you improve forecasting accuracy, which is crucial for inventory management. By optimising your warehouse, you can gain better visibility into inventory levels, demand trends, and order fulfilment rates. This can help you make more informed decisions about inventory management, reduce stockouts, and improve customer satisfaction.
Boost Productivity
Warehouse optimisation can help you boost productivity by reducing the time and effort required to perform routine tasks. By eliminating redundant processes, improving workflows, and optimising space utilisation, you can increase throughput, reduce cycle times, and improve order fulfilment rates.
Streamline Operations
Warehouse optimisation can help you streamline operations by reducing the time and effort required to perform routine tasks. By eliminating redundant processes, improving workflows, and optimising space utilisation, you can increase throughput, reduce cycle times, and improve order fulfilment rates.
Enhance Visibility
Warehouse optimisation can help you enhance visibility into your warehouse operations, crucial for effective inventory management. By implementing real-time inventory tracking systems, you gain better visibility into inventory levels, demand trends, and order fulfilment rates. This helps you make more informed decisions about inventory management, reduce stock-outs, and improve customer satisfaction.
Working with a warehouse consultant and specialist with practical experience in this area allows you to concentrate your focus on manufacturing functions while inventory and upstream supply chain is optimally serviced is managed by a trusted partner. At Acorn we take a holistic view of your supply chain needs, and how best to integrate, consolidate or outsource your inventory needs rather than attempting to fit 'a square peg in a round hole'.
Warehouse Challenges and Solutions
A well-oiled warehouse needs to be finely honed, grounded in experience and expertise, and iterated upon with real-world battle-testing to give confidence it is up to the job. Common challenges arise, let's address them in turn.
Inventory Location Problems
One of the most significant challenges of warehouse management is inventory location problems. This can lead to inefficiencies, delays, and errors in order fulfilment. To overcome this challenge, an inventory tracking system can be implemented that uses barcodes and RFID tags to identify and locate inventory items quickly.
Redundant Processes
Redundant processes can lead to inefficiencies and waste in warehouse operations. To overcome this challenge, look to the operation of lean manufacturing principles to eliminate waste and streamline workflows. This aids reduction in cycle times, improves productivity, and increases throughput.
Inefficient Space Utilisation
Inefficient space utilisation can lead to overcrowding, disorganisation, and safety hazards in a warehouse. Want to overcome this challenge? Implement a space optimisation plan that maximises the use of available space and reduce storage costs, improve safety, and increase productivity. Be careful that this isn't over-optimised so picking and packing, and movement within the warehouse, is not negatively affected.
Inaccurate Inventory Processes
Inaccurate inventory processes can lead to stock-outs, overstocking, and errors in order fulfilment. A modern inventory management system utilises real-time data to track inventory levels, demand trends, and order fulfilment rates is essential, but is only as good as the compliance and expertise of warehouse personnel who are using it. A well run inventory process leads to more informed decisions about inventory management, reduction in stock-outs, early warning of supply problems, and ultimately smooth delivery of the materials that fuel production.
Warehouse Optimisation Essentials
What are the key essential elements needing consideration when it comes to warehouse optimisation? Well, these include warehouse design and layout, warehouse processes and procedures, warehouse management systems, and warehouse equipment and automation.
Ensure you audit all these warehouse functions.
A warehousing expert will have validated operational experience in providing the most productive use of space, reducing costs, and enhancing production value. They will ensure all these key elements are optimised to service your needs.
Warehouse Design and Layout
One of the most critical aspects of warehouse optimisation is the design and layout of your warehouse. You need to ensure that the warehousing you have employed is designed in a way that maximises storage space and minimises travel time for your employees. This can be achieved by using vertical space, implementing efficient storage systems, and designing your warehouse layout to minimise the distance that goods need to travel.
Warehouse Processes and Procedures
Complex manufacturing generally uses a large and varied amount of components so efficient and effective processes have to be in place for receiving, order picking, packing, and shipping. By streamlining these processes, failure rate for orders is reduced, BOM accuracy increases, and productivity is enhanced. KPI performance of warehouse processes need to be monitored, and will identify areas for improvement. When Acorn works with clients we find immediate improvements in KPIs for our clients, and are often only constrained by internal manufacturer issues in terms of performance.
Warehouse Management Systems
Warehouse management systems (WMS) are software applications that can help you manage your warehouse operations. These systems can automate processes, provide real-time visibility into inventory levels, and help you optimise your warehouse layout and storage capacity. By implementing a WMS, you can improve accuracy, reduce labour costs, and enhance customer satisfaction. Acorn implements AI processes to interface with our WMS to enhance order delivery and responsiveness.
Warehouse Equipment and Automation
Warehouse equipment and automation can also play a significant role in warehouse optimisation. Material handling equipment can take the form of forklifts, pallet jacks, to more cutting-edge robotic technologies. Whatever technology is used, it boils down to making sure the time and effort required to move goods around your warehouse is reduced. Automation to streamline warehouse processes can reduce steps to complete processes and reduce human error.
Safety and Human Error
Safety is a critical aspect of optimal warehouse function. If proper safety procedures are not in place, accident and injury risk increases, which can result in lost productivity, increased costs, and legal liabilities.
Make sure warehousing is safe by having it configured optimally and staffed by trained, experienced personnel. Safety procedures such as regular safety training, equipment maintenance, and safety audits need to be practiced. SOPs (standard operating procedures) to minimise the risk of human error, such as double-checking orders, use of automation systems to reduce manual handling and input into the WMS.
Whether you want to consolidate or fully outsource your warehousing, an optimal warehousing operation requires efficient and effective processes and procedures. Get the above right and you ensure peak performance and business results. If you need guidance or are looking for warehousing services, we're here to help.
Also see: A concise guide to optimising warehouse design and efficiency Learn how to add supply chain value by solving these warehouse challenges
Learn about our warehouse consulting service
Acorn's warehouse consultants can help you in redesigning and revamping your existing manufacturer warehousing, build of new storage facilities, or the optimal mix between in-house inventory storage and outsourced warehousing.
We specialise in providing the ultimate 3PL and warehouse consulting experience to OEMs, adapting our key services such as kitting and assembly to their needs.